Metalworking machines are designed for a wide variety of applications, ranging from removing slag and burrs to polishing metal products. Metal finishing (or polishing) is particularly essential when producing metal components or parts. This finishing process makes metal surfaces more resistant to corrosion, rust, and typical wear—significantly improving the quality and lifespan of metal products.
As a world leader in the metal deburring and finishing market, Apex Machine Group takes pride in delivering the most efficient and powerful metal finishing machines our industry has to offer. We offer two types of solutions for refining the surface of metals: wet and dry machines. Each provides unique advantages depending on your metal finishing needs.
Today, we’ll be walking through the differences between wet vs. dry metal finishing equipment to help you make the best choice for your metalworking projects and process:
The Differences Between Wet & Dry Metal Finishing Machines
When you’re looking at finishing machines for your metalworking shop, there are dozens of factors to think about, from pricing to performance with different types of materials. Here’s an overview of some key characteristics of wet vs. dry finishing machines to help get you started.
Dry Metal Finishing Machines
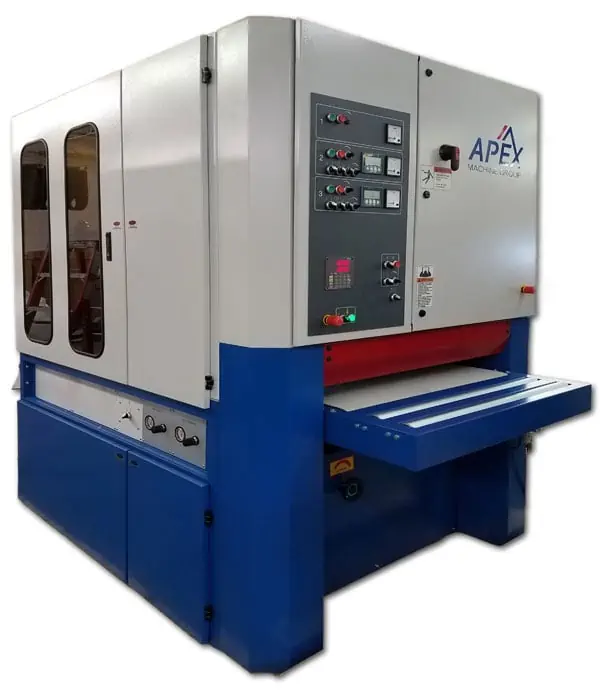
Dry machines are usually less expensive than wet solutions. They also typically require less maintenance—and feature a longer lifespan overall. (With good care, these machines can last up to 24 years.) Dry machines must be cleaned regularly to maintain effective function, which is usually done with a vacuum system.
The main drawback of dry metal finishing is that it requires some form of a dust collection system. As the machine polishes metal, it releases particulate into the air. Mixing in combustible metals (like aluminum) with steel can also introduce the risk of sparks catching fire. Fortunately, we offer extremely powerful industrial dust collections systems to combat this threat.
In short, dry finishing machines are well suited for shops that consistently process similar, non-flammable metals like steel. For the best results, we recommend choosing dry machines that offer highly accurate finishing. For example, our 2000 Series Dry Metal Machines can provide individual cam adjustments down to .001″ per head. These flexible solutions can also be outfitted with one- to four-head configurations (with drum, brush, disc, or combination heads) to suit your specific finishing projects.
Wet Metal Finishing Machines
Wet metal finishing machines can last up to 15 years when maintained correctly. They’re often more expensive than dry machines as well, but more than make up for that cost in quality and convenience. Wet machines actively spray coolant on each workpiece as it passes through for finishing, which rinses out debris and prevents the accumulation of particles. This coolant feature also removes the need for a dust collection system.
Because significantly less heat is applied vs. the dry process, parts finished by wet machines cool faster and come out clean. Additional benefits of wet metal finishing machines include their long abrasive belt life and sheer quality of finish.
Like dry machines, wet machines must be regularly cleaned and maintained to maintain effective function. These machines are ideal if your team polishes different types of metals, needs to save space in its shop (dry machines feature a larger footprint thanks to dust collection systems), or simply wants the most effective finish across its metalworking.
The Bottom Line on Wet vs. Dry Metal Finishing Equipment
While polishing can be successfully obtained using either wet or dry finishing machines, the wet process is typically preferred. Wet machines get the best results when polishing and finishing metal materials. For example, our 1000 Series Wet Metal Machines have a smaller footprint and a cooler running process. These solutions can also be customized with a wide variety of head configurations and types, including drum, brush, and disc heads.
However, that’s not to say that dry machines are the wrong choice for your project. These metal finishing solutions are typically less expensive than wet machines—and can last up to twice as long if cleaned, lubricated, and cared for properly. We encourage you to reach out to us if you’re still unsure which process will work best for your metalworking operations. Our experts can walk you through pricing, maintenance, performance, and everything else you need to choose the right machine for your needs and budget.
Perfect Your Metal Finishing with Apex Machine Group
Apex Machine Group offers a leading selection of wet and dry metal finishing machines to match your shop. We can help you create uniformity and efficiency across each finishing process—no matter how demanding the materials or conditions. Whether you’re finishing stainless steel, aluminum, copper, or even titanium, we’ll match you with the perfect machine for your needs.
To get started on purchasing a solution, please reach out to an application specialist today. We look forward to working with you.